ISO 9001:2015 roles and responsibilities
We all know that human resource is the most important assets that any organization has. Within the current version of ISO 9001:2015 roles and responsibilities are discussed in multiple clauses within the standard, including 5.2 (assigning and communicating roles), 7.1.2 (allocation of staff to meet requirements), and 7.2 (competence and training).
The business world, over the past decades, has evolved from Henry Ford stating that “you can have a car any color you like, as long as it’s black”, to highly customizable solutions required by customers. From a world of mass production, where everything was done in the same way, to flexible products, for highly demanding clients.
Moreover, businesses have evolved from a world dominated by the manufacturing business, to an increase in service based businesses. From a complete monopoly by local businesses, to a international marketplace whereby local businesses are competing to their international counterparts.
Invariably, this has led to an increased level of service that customers expect in their purchasing experience. Not that I need to explain why running a business has become more sophisticated in recent years, but I wanted to demonstrate that archaic methods cannot be used to run a modern, successful business.
Regular organizational charts are one of the old methods that are used to demonstrate how a business works. Indeed, organizational structures are useful to give a clear picture of who reports to whom, that is certainly needed in large organizations (that employ hundreds of people), however less needed in a company of, say, 25 employees, which is the size of most companies in Malta, and indeed the size of most companies I’ve worked with.
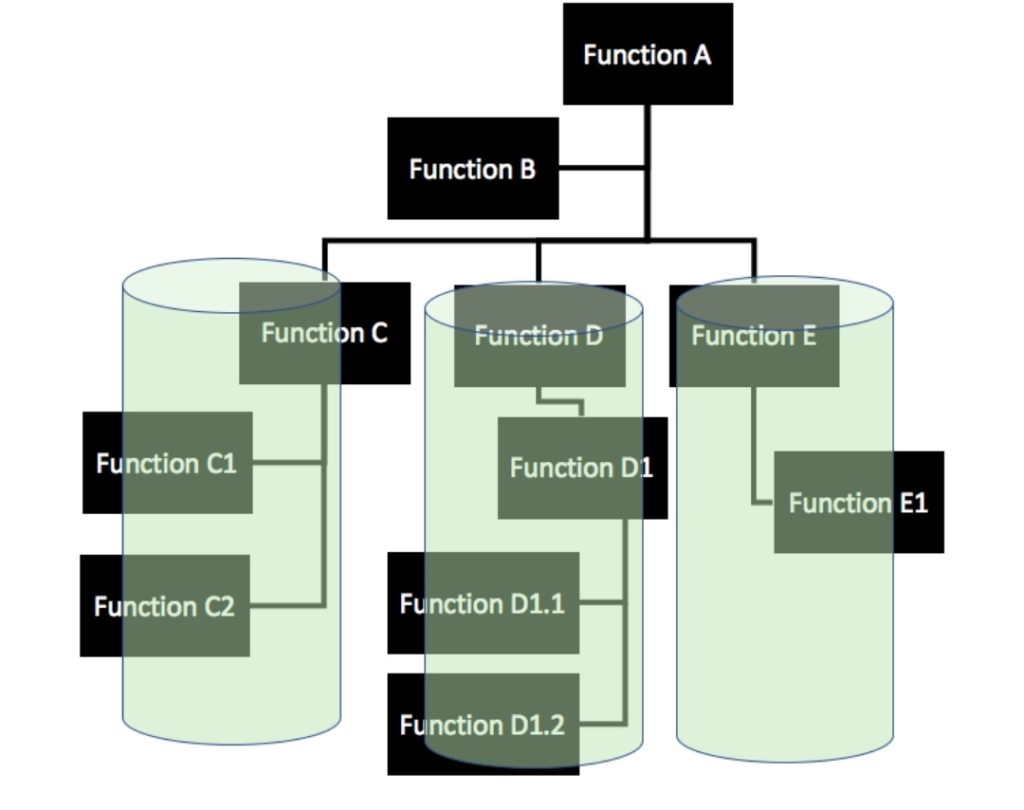
The image above shows that when smaller companies use organizational charts, they are probably doing more harm than good. They are creating silos (depicted by the vertical cylinders) between the various functions of the organization. Such silos create multiple problems, including:
• lack of accountability
• decrease efficiency in communication
• gray areas, which seem to be no one’s responsibility
• internal politics and possibly friction between different departments
• different priorities for each function, and hence not everyone pulling the same rope
• bureaucracy
• the need for more managers
• harder to establish KPIs and objectives
… and others
The process approach that ISO 9001:2015 promotes a radically different approach. It encourages organizations to start from the customer, and note the processes that are needed to deliver the end result required.
By first noting the processes the needed to serve the customer, and then defining who will be responsible for what, and who reports to whom, it will be easier to maintain a flat, lean organization.

As per the image above, when working on ISO 9001:2015 roles and responsibilities, by first keeping the process in mind, and then defining the organization chart, business leaders can assign responsibilities accordingly.
I have used this approach in all my businesses, such as Kraze Travel – adventure travel agents in Malta.
If you are seeking to get ISO 9001 certified fast, get in touch with us. Or else, you can simply click here to get a quote for ISO certification.
FAQ about Roles & Responsibilities as per ISO 9001:2015
Question: I’ve been doing your course on ISO 9001:2015 and was wondering. Do responsibilities/roles need to be documented in the QMS? I’ve recently received a minor for this but explained to the auditor that the roles & responsibilities are detailed on the individual’s job description (kept by HR). The auditor said that the authority needs to be on the QMS eg: who can stop the production line in the instance of defective parts being produced. Is this correct?
Answer: Clause 5.3 – Organisational Roles, Responsibilities & Authorities states that “Top management shall ensure that the responsibilities and authorities for relevant roles are assigned,
communicated and understood within the organization.
Top management shall assign the responsibility and authority for:
a) ensuring that the quality management system conforms to the requirements of this International Standard;
b) ensuring that the processes are delivering their intended outputs;
c) reporting on the performance of the quality management system and on opportunities for improvement (see 10.1), in particular to top management;
d) ensuring the promotion of customer focus throughout the organization;
e) ensuring that the integrity of the quality management system is maintained when changes to the quality management system are planned and implemented”.
With this in mind, the standard does not state who is the person should be responsible for taking certain decisions. For example, and as per your question, you stated that “authority needs to be on the QMS eg: who can stop the production line in the instance of defective parts being produced” – does that mean an operator seeing defective parts should not have the initiative to stop the production? Certainly not. As per Clause 5.5, the part of the role of top management is to “engaging, directing, and supporting persons to contribute to the effectiveness of the quality
management system” – and that certainly does not relate to the quality Manager.
May I remind you that ISO 9001:2015 Certification can be obtained by companies operating in all industries? Not all companies employ the same number of people, and smaller organizations may not employ someone who is only committed to Quality – more of then than not – Quality is a responsibility shared by many people.
8 Comments
Comments are closed.