5 Steps to Implement ISO Quality Management System
Implementing ISO is not an easy task, I get it. Some companies view this as a mission impossible, a task so big and challenging that is not even worth considering. But what if I had to tell you that you can take these 5 super easy steps to take a big leap towards ISO success and implementing an ISO quality management system?
Step 1 | Set up a team for implementing the ISO quality management system
If you are serious about implementing ISO in your organisation, then you must have a team. A team made of several people with a variety of skills who come from different levels of management is critical. If you are a Quality Manager, then you must include yourself. You must have people from different levels of the hierarchical structure to be successful.
So you might be asking, but why have a team, can’t I implement the ISO quality management system by myself? Here are some reasons why you need this team:
- Having people from different levels gives you a more varied perspective of all issues that occur throughout the organisation.
- Employees who are facing these issues may have a better solution than top management individuals.
- Having a team comprised of different individuals coming from different levels of the organisation is more likely to minimise employee resistance to change.
Step 2 | Train people and create training plans to ensure everyone is on board the ISO quality management system
Allowing people to carry out tasks without proper guidance is irresponsible and dangerous to the operations of the company. Employees must therefore be trained to meet the demands that may shift as a result of the introduction of the ISO quality management system.
If employee A receives no training on the changes in the process of issuing an invoice, then this employee will be working against the scope of the organisation. Don’t you agree? Even if these actions are done unwillingly, harm can still be done. So training is essential.
Having an effective training plan in place will also be critical when your organisation comes to employing new individuals. The same level of quality can only be attained by training the new employees. Hence, achieving a uniform level of quality through the power of the ISO quality management system.

Step 3 | Create the scope for the ISO quality management system
The scope of certification is perhaps one of the most underrated aspects when working towards ISO certification. You see, when implementing an ISO standard, you need to know what part of the organisation you are going to improve.
So, let’s put an example to make more sense of what we just went over.
Say your company deals with the manufacturing and distribution of vehicles and offers repair services amongst other types of non-essential vehicular services. Naturally, your organisation will have plenty of processes, each dealing with the different aspects of the company. Taking the manufacturing and assembly line alone, you are bound to end up with tens, if not hundreds of smaller processes. As a result, you cannot be ISO-certified in all aspects of the organisation. In this case, the scope of certification for the ISO quality management system may be the manufacturing and assembly line.
Now, this is important as it will determine future events. Sounds a bit dramatic? Sure, but hear me out.
If you put down that your scope of certification is the manufacturing and assembly line, then you are not going to be asked about the distribution of the vehicles throughout the various countries. Similarly, you won’t be asked about the other services which you provide to customers. These are not part of the scope of certification. As a result, no certification body will ask you about the processes relating to areas that do not form part of the scope.
So, to sum up this section, you need to have a scope and ensure to put your energy into what you have mentioned there. That is what will make or break your success in achieving ISO certification.
Step 4 | Don’t fall into the bureaucratic traps of ISO
Bureaucracy is a concept that is sometimes difficult to understand and identify. You see, bureaucracy is the opposite of having an effective ISO quality management system. Mind you, an ISO certification can still be obtained, even if you have an excessively bureaucratic process in place. It just makes the world harder. Personally, I find the world is already a tough place, so why make it any tougher?
You see, having documentation is sometimes a necessity. but is it always required? When I first started out my career, I was working at a place where they had an overly bureaucratic system in place. In order to get something done, I had to go through numerous processes and paperwork. From a whole working day, I would’ve ended up getting tired after finishing 1 single task – the very first one of the day! This is wrong on so many levels.
Of course, the other side of the spectrum is no better. I have also worked in places in the past where no task is done the same way twice. Frustrating, no?
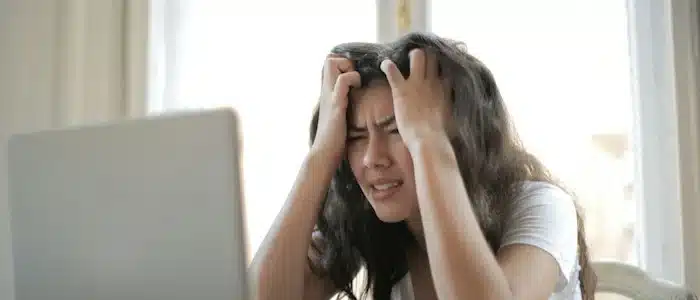
So, what I’m saying is, that you must have documentation, but only that which is deemed necessary for the success of the ISO quality management system.
Example…
So if you are, for example, hiring someone new, you need their personal information and maybe some references from their previous employers and sometimes even their portfolio. But do you actually need to know the grades of the Maths class of their post-secondary education?
Another example is the issuing of an invoice. To issue an invoice, you need to have some level of detail. But does the invoice need to be 5 pages long? Do you need to get the approval of 2 senior members of the sales team to issue an invoice? And what happens if those people are not present to approve these invoices? Will the operations come to a halt?
Step 5 | Following through with the system
This section is perhaps the easiest to explain and the toughest to actually perform. But it’s useless setting up yourself for a successful ISO quality management system and then failing to stick to it. If you are doing an ISo standard, you cannot just do it for the sake of the certification. THAT would indeed be a waste of time, money and human resources.
You must aim to achieve ISO certification simply because you want to have a better organisation. You want to stick to an ISO quality management system simply because you want to have an improved product. Moreover, you want to better understand what the stakeholder needs.
After all, the motto for an ISO quality management system is to strive for perfection, even if you are knowingly aware that perfection is never a realistic target.
Where can you learn more about ISO quality management system?
Did you know about my Youtube channel about ISO? Go check it out and go through my other articles to learn more about the internal and external issues when implementing ISO and understand more about the pitfalls of ISO.