Good Distribution Practise (GDP) Certification in Malta
GDP Certification in Malta refers to the minimum standard that distributors of wholesale products must meet to ensure that good quality medicines are maintained throughout the supply chain.
Unlike an ISO certification, GDP is a mandatory requirement for companies involved in the wholesale, or distribution of medicinal products. Even more so, now with the introduction of a new Medical Device Regulation for Malta and all other EU Member states. Even though the application of the management system might vary, the design of the management system would be quite similar.
Why is a GDP Certification required?
Compliance with GDP ensure that:
- companies operating with the supply chain of medicinal products are in accordance with EU legislation
- medicines are kept at the right levels of temperature, humidity and methods of handling, throughout the lifecycle
- the medicinal products are not contaminated
- products within the care of licensed wholesalers aren’t kept for a long period of time within storage, and are therefore consumed well within their expiry date
- the right products reach the right product in a timely manner (the definition of a quality service)
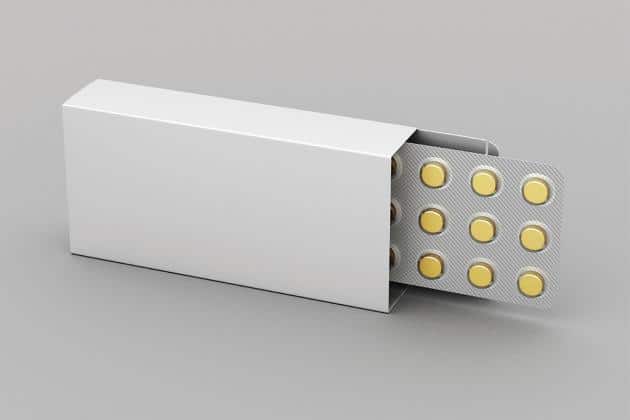
Guidelines on the principles of Good Distribution Practices
The following are the elements of the management systems that must be catered for companies involved in the distribution of active substances for medicinal products for human use, and which therefore need GDP Certification in Malta.
Quality System
A management system is “the way in which an organization manages the interrelated parts of its business in order to achieve its objectives”. The following elements of the management system must be defined and actioned by the company to ensure that the company:
- has defined responsibilities for the personnel of the company
- has identified the risks and opportunities within its processes
- the organization shall appoint a medical device registered person (MDRP), who is responsible for the organization’s quality system
- has set out a quality policy with clear quality objectives
Human Resources / Personnel
Given the nature of the operation of companies involved in the distribution of medical substances, GDP gives are more clear requirements than the clauses of ISO 9001.
The distributor must have a person who is responsible to ensure that all elements of the management system (as described on this page), are adhered to. The roles and responsibilities of the responsible person must be defined in writing, and the person must have adequate training to ensure that they are knowledgable about the specifics of their role.
“Every licensed wholesale dealer [of pharmaceutical products] must appoint a Responsible Person who is ultimately responsible for ensuring that an effective quality system is in place. In Malta, this person must be a pharmacist registered with the Pharmacy Council” source: Malta Medicines Authority
Documentation
Given the nature of the business, wholesalers of medicinal products must have written procedures for the key processes within their business, as part of the organisational knowledge.
Particularly, documentation relating to the compliance of the elements mentioned within the page must be readily available to all employees in a way that they could understanding.
Procedures should include:
- receipt and checking of deliveries
- storage, cleaning and maintenance of the premises )including pest control)
- recording of storage conditions
- security of stock on-site and during transportation
- withdrawal of medicinal items from saleable stock
- handling of return products, including plans for recall.
Records to keep include:
- identity of the supplier, original manufacturer, shipping agent and/or consignee
- address of the supplier, original manufacturer, shipping agent and/or consignee
- purchase orders
- bills of lading, transportation and distribution records
- receipt documents
- name or designation of the active substance
- manufacturer’s batch number
- certificates of analysis, including those of the original manufacturer
- retest or expiry date
Premises and equipment
The premises used should be designed in such a way that it protects the medicinal products being handled. Namely, it should:
- provide protection from any chemicals or materials that might affect the suitability of the medicinal products.
- have lighting, temperature, humidity, and ventilation that does not adversely affect the quality of the products or the accurate functioning of monitoring equipment.
- in the case of special storage conditions, specific areas shall be suitability equipped and constantly monitored with tracking records kept and available.
- refrigerated areas and cabinets must be regularly cleaned to prevent the growth of mold.
- specific segregated areas, clearly market, should be provided for the storage of products in quarantine, rejected, returned, or recalled products.
- to prevent unauthorized access
Moreover, any monitoring devices (such as weighing scales, thermometers etc) must be calibrated, to ensure reliable readings. Certified traceable records are necessary.
Operations
Unlike with ISO Certifications, a GDP Certification clearly states the areas of operation that need to be defined. The guidelines go into the details of what is actually required by the wholesaler of medicinal products.
The processes that need to be conisdered are:
- Orders
- Receipt
- Storage
- Deliveries to customers
- Transfer of information
Returns, complaints and recalls
Any business, no matter how many systems are in place, is bound to have some kind of quality issues. The role of a strong management system is to identify, trace, and mitigate such issues.
The possible presence of non-compliant and counterfeit medical devices in the market is a constant threat to the health and safety of users, patients, and the public. Non-compliant devices may carry false or misleading claims with respect to performance, compliance with legislation, or fitness for purpose.
A GDP Certification in Malta requires a specific way in which returned active substances should be identified to ensure proper isolation. Moreover, details on the information that is required for all returned medicinal products.
Similar to the correct actions that are required for ISO certification, a CAPA is required to ensure that the corrective actions are taken whenever a complaint is received. A strong management system would ensure that the DMAIC process is followed:
- Define
- Measure
- Analyse
- Improve
- Control
Self-inspections
Commonly referred to as Internal Audits, a GDP Certified company must do self-inspections to ensure that the guidelines defined in this page are followed. Naturally, any deviations from the above conditions must be handled as any other complaint would.
2 Comments
Comments are closed.