Supplier Management for ISO 9001 Certification
Handling your suppliers within your value chain in a systematic fashion is extremely critical to ensure a high-quality product or service. Supplier Management for ISO 9001 Certification is an easy requirement of the ISO 9001 standard that does not require too much effort from your end – and yet that will leave long-lasting benefits to your business.
Which suppliers to manage for ISO 9001 Certification?
The suppliers that are to be considered are products and services being supplied which are important to the management of the quality of our products and services.
To be able to explain my point in the most understandable way I would like to start off by sharing with you the screen which is an excerpt of the standard. When it comes to supplier management for iso 9001 the requirements are gathered in clause 8.4 of the standard. Here, the standard tells us that basically we should determine the controls that are to be applied to external providers of processes products and services in three particular reasons
Incorporation into the organization’s own products and services
When we are buying products and services and incorporating these products and services to our own products and services. So if for example we are buying a certain product and reselling it or modifying that product and reselling it then the suppliers from which we are buying, those products and services have to be included within the management of suppliers
ISO Frog | The Latest Project From Luke Desira
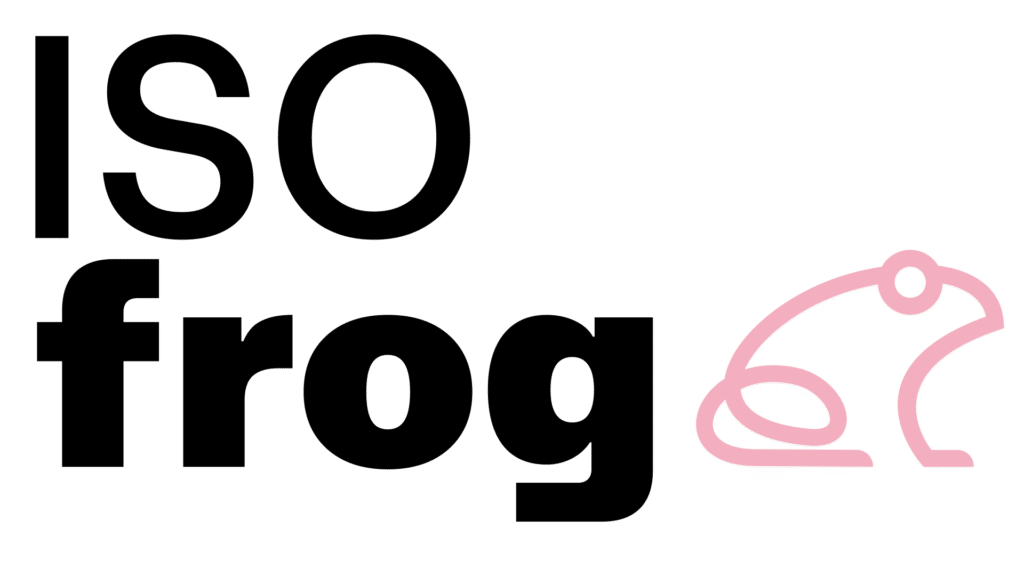
ISO Frog is the new solution for ISO Certification. This software is crafted by a team of ISO experts, led by the management systems specialist, Luke Desira.
Managing suppliers effectively is key in maintaining quality, and ISO Frog makes this process more manageable. The software includes supplier management tools that align with ISO 9001:2015 Clause 8.4, allowing you to evaluate, select, and monitor suppliers with ease. With ISO Frog, you can ensure that your suppliers meet your quality standards, track performance, and maintain necessary documentation, all in one place. Gain peace of mind with ISO Frog.
Sign up today and be one of the first to gain early access to ISO Frog itself! You’ll be effectively helping us test ISO Frog. By signing up, you’ll be receiving:
Provided directly to the customer(s) by external providers on behalf of
the organization
When products and services are provided directly to the customers by external providers okay so in this case we are considering scenarios where the company does not even receive the product or services themselves and then make an any necessary adjustments and send them to the client but instead the products are shipped or are delivered straight to the customers. In this case we can consider that the suppliers are acting on our behalf and therefore yes definitely we have to consider suppliers when it comes to products and services that are delivered straight to the customer.
Process provided by an external provider
We have to consider the evaluation of suppliers for processes or part of processes that are provided by external providers that form part of the integral way in which we work as a company. Just to give you an example of the first instance let’s say that we are a wholesaler of food and of food and beverages therefore the supplier the from where we buy the food and beverages would be considered as an external provider that we have to evaluate. Another instance is where for example we are sending and we are a contract contracting company and we do not do the actual work ourselves but we subcontract all the activities for example without new subcontract builders and in this case since the builders are acting on our behalf as contractors. Then we have to evaluate the performance given by our subcontractors. Or if for example part of the invoicing process is being handled by an accountancy firm then that accountancy firm falls part of the processes within our quality management system and we have to make sure that the products and services being supplied by this external provider are actually important and we have to evaluate the performance of these suppliers.
An example for suppliers to consider for a service comapny
Let’s take the example of a travel agency in Malta. The type of service that will be offered by the supplier will determine the extent to which the evaluation will include.
- Offering ancillary services – stationary, office leasing.
- Offering supporting processes – accounting, marketing, HR etc
- Offering key processes – tour agents in foreign destinations offered by the travel agency
In the above example, we are only required to manage suppliers offering key processes. Even though without accounts, HR or stationary the company will not run effectively – they are not directly involved in delivering the service to the customers – and therefore, as such, the standard does not make it a requirement to perform Supplier Management for ISO 9001 Certification for such suppliers.
How will ISO 9001 help you choose your suppliers?
ISO 9001 will not tell you which suppliers to work with. Supplier approval and evaluation requirements are defined by the company. What the standard asks for is that we ensure that we are working with the right suppliers for our business. And we do not have to consider all the suppliers. If for example we are using stationery and we do not resell that stationary then we do not need to necessarily include the supplier of stationery for our company but if we feel that without stationary our products and services might have problems then it would be wise to make sure that we are getting the supply and delivery of stationery products within the scope of the supplier evaluation that we are considering for suppliers.
Supplier Approval
Before working with any supplier that will provide products or services that are directly value-adding to our own product offering, we must make sure that the suppliers are adequate. Different industries take this supplier evaluation to different levels of accuracy. For example, the automotive industry employs the PPAP (production part approval process) to manage suppliers.
A regular ISO 9001 Certification will require much less effort to approve a supplier. For example, if the suppliers is local, you can visit the supplier and see their offices or production plant. Or, if you have a business relationship (without conflict of interest) with the supplier – whereby you’ve been working for a number of years. Or you can ask the supplier for certification (including ISO Certification) to get reassurance that the company is capable of delivering the product or service as required.
Supplier Complaints
While running the quality management system, a professional Quality Manager will always be on the lookout for actions for continual improvement. As discussed in ‘corrective actions and non-conformities within ISO 9001‘ there are 3 types of complaints:
- internal complaints
- customer complaints
- supplier complaints
Naturally, here we are referring to the latter. Whenever a supplier does not meet our requirements, we can file a supplier complaint. Examples of supplier complaints include:
- delivering defective products
- delivering products late (thereby missing deadlines)
- not respecting customer property
- not respecting the clients by being rude
As can be seen above, anything that doesn’t please us, and the way we like conducting business can be included as a supplier complaint. A supplier is there to help us achieve the mission we’d set out in the Quality Policy – and apart from being aware of the quality policy, suppliers must live the values as shared within our company.
Which clause in ISO 9001:2015 addresses the requirements for suppliers?
In clause 8.4.1 we get information about what do we have to do as regards these suppliers.
The standard says that the organization shall determine and apply criteria for the evaluation selection monitoring of performance and re-evaluation of external providers based on their ability to provide processes or products and services in accordance with requirements. The fact that this information shall be retained as documented information indicates that we have to have some kind of reports some kind of information where we are storing this information.
What is an approved suppliers’ list and how to create one
How do we apply this in practice? The way I approach this with my clients is that first of all we create a list of all the suppliers that are critical to the operation of the company as I have just explained. And then I would explain what type of products and services do these provide. I also like to give an estimate of the years of collaboration we have with each and every supplier because this helps us to provide context that we have been working with these suppliers for quite a long while and especially suppliers with whom we have a long-standing relationship, then we certainly do not need to approve these suppliers once again. However for new suppliers, especially for critical suppliers, it might be wise to first create some kind of system where we are going to evaluate the performance of our suppliers before actually moving forward and approving these suppliers.

Criteria for Supplier Evaluation in ISO 9001
We have to identify certain criteria on which we would like to evaluate the performance of our suppliers. For example, lets’ take three attributes:
- product quality
- value for money
- complaint handling
This doesn’t necessarily have to be your selection of criteria on which you evaluate your suppliers. You can also have more criteria on which you evaluate your suppliers but the important thing is to have some kind of metric some kind of criteria that will we are able to evaluate our supplier.
Rating for Supplier Management in ISO 9001
We would want to give each and every of our suppliers a rating from one to five to evaluate their performance. 1 would be lowest, and 5 highest. Based on this information especially if we start comparing this information here over here over here then we can get information about the performance that our suppliers are giving us, and that is the first topic and the most important topic when it comes to supplier management for ISO 9001.
An example of Supplier Management in ISO 9001
At a pre-determined frequency – most companies choose to do it once a year (you can do it more frequently, but not less frequently) – the management of the organisation must evaluate their suppliers. Unless the company is very small, and they have a quasi day-to-day contact with the supplier, the only way to get the data to evaluate a supplier is through the supplier complaints.
Alas, at supplier evaluation, we can choose any criteria we’d like on which we’d like to rate our suppliers. We can also give importance ratings to each metric – to help us ensure that the suppliers are delivering on the factors that matter most to us, our business, and most importantly, our customers.
Some metrics that companies use to evaluate their suppliers include:
- pricing
- quality
- deadline
Does ISO 9001:2015 require a supplier audit?
No, ISO 9001 does not require a supplier audit. In this blog, I am explaining all that needs to be done for supplier management as per ISO 9001. We do not need to go overboard with this management of suppliers when it comes to iso 9001. It is good for us to ensure that the quality of the processes and products of our suppliers meet our requirements.
Instead of auditing suppliers, we can check product quality
So the first requirement is to define the controls that we intend to apply to our external providers. If for example, we are receiving physical products from our suppliers so that we can resell we can identify some kind of statistically significant sample size where we are going to evaluate and check the quality characteristics of the products that we are purchasing.
We also have to take into consideration the potential impact of the externally provided processes products and services on our organization’s ability to consistently meet customer applicable statutory and regulatory requirements. it is important to keep in mind that whenever we are subcontracting a product process or service we are still liable for any problems that our supplier might cause. And therefore it is wise for us to apply specific and control measures to make sure that our suppliers are consistently providing a high-quality product or service to our clients.
Finally, we also have to determine the verification and other activities necessary to ensure that the externally provided processes products, and services meet requirements. In this case, they would be our requirements for systems that we are going to put in place to ensure that the requirements of suppliers are being met, for example through audits, asking for ISO certification, or any other system.
Corrective actions and supplier management in ISO 9001
As you might be aware the corrective and prevent preventive action system is one of the most important criteria and elements within our quality management system. This is basically the way we will in which we will be monitoring anything that didn’t go well within our company. Granted the corrective actions are typically used for customer complaints or also for internal issues within the company however sometimes we might also have problems with our suppliers for example:
- due to shipments arriving late
- short shipments
- it can be that the items were delivered and were damaged while they were being delivered
- it can be that one of the employees of our subcontractors was rude to our clients and our client was offended and they contacted us
Benefit of monitoring supplier complaints
All of these are elements that can go wrong from the supplier’s point of view that will have a direct impact on the quality of our organization. If we keep track of such issues that are being caused by our suppliers within our corrective and preventive action system, then we are going to keep start keeping a track record of the performance of our suppliers. The way I like to have this corrective and preventive action system in place is typically through a simple excel sheet. For example a supplier complaint on a particular day.

In this case, the problem was that the cabinet buzzer was not working. And we would write the name of the supplier so that at the end of the year we would be able to count the number of non-conformities or corrective actions that were caused by each individual supplier.
Then we can go on with the standard process for handing a corrective action where we:
- identify the action taken to solve the problem in the short term
- identify the root cause
- implement and action to solve permanently and define the date of implementation
- assign responsibility and find the date in which we are going to control that the implemented the action item that we have found to the particular solution to solve the root cause of the problem.
Factual approach to decision making – on supplier management
By keeping track of the non-conformities of all problems that are caused by our suppliers within our quality management system, we would be in a position to count the most common sources of issues. This helps us to have the right information that we need, to guide us through two different scenarios:
- Defect for one specific supplier: for example if we note that one particular supplier is having a high rate of defective products then within the supplier evaluation we can say that the product quality is low. This doesn’t necessarily have to be an opinion of one individual person or of a team of people but rather if we compile the information within the corrective action then we are taking factual approach to decision making when it comes to supplier evaluation.
- Evaluating the performance of suppliers (which can also be an example of a quality objective for ISO 9001:2015) – By discussing the information within the corrective actions list with an open mind during the management review meeting then we are bound to always work with the right suppliers for our specific organization.
Supplier information
Finally, when it comes to the supplier management for ISO 9001 we also have to consider the information for external providers. Just like in Clause 8.2 – the sales and marketing process in ISO 9001 within the standard where we are making sure that we are gathering all the information needed from our customers to make sure that we understand exactly what they need from us we are also going to make sure that we are communicating with our suppliers in an effective manner whereby we are communicating with them or our requirements in an explicit way. This is for us to make sure that our suppliers provide us with the right products services or processes that are needed for our organization.
What are the benefits of Supplier Management in ISO 9001?
Based on the above, we have seen tangible facts on how collecting specific data can help us to have data relating to supplier management, based on ISO 9001 principles.

Supplier management is one of the items on the agenda that we have to discuss during the management review meeting for ISO 9001:2015 and therefore it’s an excellent opportunity for us to evaluate the performance of our suppliers to make sure that the services and products that we are getting from our suppliers meet the demand of our customer and of our organization.
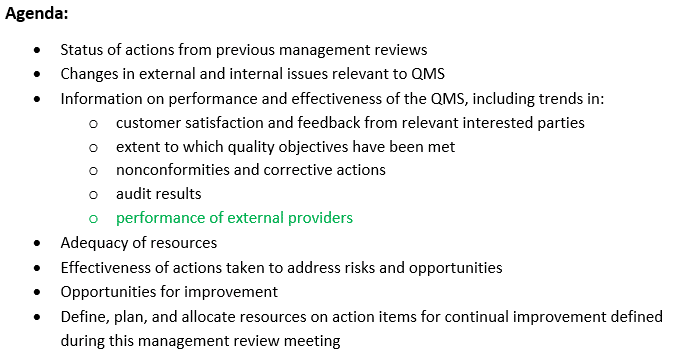
With this mentality, we are achieving a system of continual improvement. Just like we ask our customers to give us an evaluation of how they feel that our products and services have met their needs, we are also seeking to get information about how our suppliers managed to meet and exceed ideally our expectations.
This evaluation of the suppliers does not necessarily have to be communicated with our suppliers but the most important thing is that as i have discussed this evaluation of suppliers will be one of the topics of the agenda within the management review meeting so that then year over year we would be in a position to evaluate the performance of our suppliers and if we feel that one of the suppliers is reducing their performance to our organization or if we feel that our supplier for the past year has not performed as well as we wanted, then we would have the data to take the appropriate action.
Conclusion on Supplier Management for ISO 9001
And that’s all you have to do to meet the requirements for supplier management in ISO 9001. I hope that you found this explanation useful and that it will help you to further grow your knowledge about ISO 9001. if you would like any further information please feel free to get in touch with me personally at hello@lukedesira.com and I would be very happy to help you out with any questions that you might have as regards ISO 9001.
2 Comments
Comments are closed.